Processing Q&A: Coperion's new Food, Health and Nutrition group
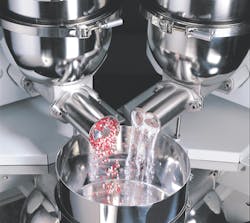
Sharon Nowak is Global Business Development Manager for Food and Pharma at Coperion K-Tron. Processing recently spoke with Sharon about recent company acquisitions and the creation of Coperion’s new Food, Health, and Nutrition (FHN) group.
(Note: This conversation has been edited for space and clarity.)
Q: For those who aren't familiar with Coperion, what types of equipment does the company manufacture and what industries do you primarily serve?
A: Coperion is a global industrial and technology manufacturing company who design and engineer systems and solutions for the food, health, and nutrition markets, as well as for polymers and chemicals. Including both new technologies and aftermarket sales and services, our areas of expertise extend to compounding and extrusion systems, sorting shredding, and washing equipment, as well as material handling of bulk solids with conveying mixing, milling, and feeding technologies. Coperion employs about 5,000 people at 50 locations worldwide, and as a part of that, I am Global Business Development Manager for the food, nutraceutical and pharmaceutical industries.
Q: In the last couple of years, Coperion’s parent company, Hillenbrand, has acquired several companies, including Schenck Process Food and Performance Materials and its brands Kemutec and Baker Perkins, as well as the Linksys group. How have these acquisitions impacted the markets you serve? And what are the benefits to customers?
A: The recent acquisitions have definitely brought an enormous depth of technical expertise as well as innovative equipment for the food, nutrition/pharma, plastics, chemical, and battery industries. In the FHN group, which is food, health, and nutrition space, the addition of technologies designed for the growing markets of confectionery, bakery, plant-based products, and pet food has allowed us to provide complex systems with all solutions provided from one source and specifically designed for the application.
In addition, for the highly technical requirements of the pharmaceutical and nutraceutical markets, Coperion can now provide specialized systems for both batch and continuous processing. Whether it is choosing the right mill for the application through our Kemutec powder processing technology experts or the high-performing mixing technologies as offered through our Baker Perkins, VMI, or Diosna brands, the system experts of Coperion can now ensure that the proper technology is applied for the application. This, of course, presents a tremendous advantage and confidence for our customers, as they can now rely on a one-source supplier, all backed by our extensive global aftermarket service team.
Q: What are the most common types of feeders for bulk solids processes? And how do end users determine which type to use for a given material and application?
A: There's a wide variety of feeding technologies out there, everything from screw feeders to trays to conveyors, and they're all basically geared to specific applications. The acquisition of the Schenck Process Food and Performance Materials brand of feeding technologies has helped expand our product offerings even more. So, Coperion now can offer belt feeders, vibratory tray feeders, single- and twin-screw feeders as well as rotary valves for feeding applications. And all of these feeder technologies are available in a variety of design executions, including the more standard design for plastics and chemicals all the way up to hygienic and/or high-containment designs for industries like pharma or the battery market.
First and foremost, what we look at when a customer comes to us at Coperion for a feeding application is the material properties of the product to be fed. We don't want to force feed a technology to the wrong application based upon the specific properties of the material. For example, cohesive powders may be better suited for a twin-screw application. On the other hand, if you have a friable material, like plastic pellets or inclusions for food applications or granulations or even finished tablets for the pharma industry, that may be better suited for a vibratory tray or a belt feeder type design.
Another critical aspect that we consider is the level of accuracy required in the feed, which will determine whether gravimetric or volumetric feeding is acceptable, as well as whether this is a batch dispensing or continuous feed application. Finally, it's important that any feed technology application takes into consideration not only the properties, but also the installation requirements, such as the frequency of cleaning, the containment of a potent compound — for example, we have feeders in the industry that are actually feeding high-potency materials for cancer drugs, which are extremely toxic and cannot have any interference with the operator. Another area is space limitation. There is usually never enough height when you're trying to install a feeding operation and also the refill that goes into it. So, we want to look at that as well.
And then things like explosive handling properties are very important when we're dealing with materials like flour and sugar that have explosive handling issues when they are in a pneumatic conveying line, for example. So, we want to make sure that whatever we do for the refill of that application is designed so that we don't have any issues. And like I said, trying not to force the fit, we want to focus on the technology and get the right technology, because that will be very important as far as the customer's product quality, but also it will affect the customer’s ROI of the complete process, which obviously everybody is very concerned with these days.
Q: In recent years, there has been a trend in pharma manufacturing away from batch processes and toward continuous processes. What challenges has this move presented to manufacturers? And how can modern equipment help to address these challenges?
A: There have been a lot of technical articles and papers on this. As a matter of fact, the FDA is heavily pushing continuous for its advantages. Specifically, that was advanced as a result of the pandemic because continuous processing not only offers key advantages, such as ease of scaleup, smaller overall footprint, faster turnover, less inventory, and in some cases, higher quality. But as I mentioned, faster turnover, it allows you to get the drugs from development to production much faster. And then that way we can address issues like the pandemic where we have shortages or drugs that need to be developed. With continuous we can get that done as a much quicker timeframe.
But one of the biggest challenges in continuous manufacturing, whether it's what's called direct compression, where we're going right from the mixer to a tablet press, wet granulation, dry granulation, or hot melt extrusion, is the accurate feeding and refill of the ingredients, whether it's highly potent active ingredients (called APIs), that's your drug substance that's in the blend, and then the excipients. Most excipients like lactose, for example, are not free flowing. There are some APIs which are extremely difficult to feed continuously, and one of the objectives of Coperion and also of drug substance manufacturers and even excipient manufacturers is to try to alleviate the flow properties of those compounds, and then for Coperion to design equipment that will be able to help with the feeding so that you can do more on the continuous side.
We offer a wide variety of solutions for some of these difficult materials. Some of them include our innovative technology called ActiFlow, which is a smart vibration device to help with flow out of the feeder. We have modular-design feeders, where we may find that going to a larger screw and feeder size, like going from a 20 millimeter to a 35 millimeter, can help with flow issues with very low-bulk-density materials. But we'll do that all within one feeder, so you can swap those out very quickly. But there are still those drugs substances which can be better processed in a batch situation. So, whenever any continuous process is being considered, it's important to test and optimize the feeding technologies available for the specific material properties.
Another thing that's often overlooked, and usually considered after the fact, is not only to look at the feeder, but to also look at how the feeder is being refilled. This is extremely important because consistent refill is critical to any continuous process. It's important to work with a supplier like Coperion that not only recognizes the challenges and solutions available for feeding materials but can also handle the requirements and delivery of those products to the feeder and ensure that the continuous process is not interrupted.
Solutions for material handling can include proper layout of the upstream equipment, proper selection of the refill technology, and proper selection of all equipment components to ensure efficient cleaning, containment and safe operation. That was particularly important when we were developing the modular pharmaceutical feeder. Our teams on the R&D side for Coperion are constantly innovating new methods on all of our equipment to combat all of these challenges.
Another area where we get involved specifically on continuous is hot melt extrusion. That's another continuous process which is being utilized for solid dosage form production and has been shown to have distinct advantages in the production of specific compounds such as highly insoluble drug forms. This technology has been used for many years in the plastics industry and is relatively new to the pharma industry compared to more traditional techniques. In this technology, as well as in continuous processing in general, one of the key challenges is the learning curve of new engineers and operators over batch processes. In order to help with this education, Coperion offers a number of seminars and training sessions. We also do quite a lot of work with universities, where we have equipment currently on continuous systems, and they focus on a variety of technologies, including feeding, refill and extrusion.
Another key advantage of the newly formed FHN group is that Coperion can now offer not only solutions for continuous, but through our acquisition of Diosna, we now also have a full line of batch granulation and drying solutions for batch operations. So, we're very excited about being able to offer the complete gamut for applications, where it may not be applicable on the continuous side. In fact, at this year's Interphex, we're highlighting technologies for both continuous and batch processing.
(You can listen to this entire interview by going to the “Podcasts” page on the Processing website or searching for "Ear on Processing" wherever you get your podcasts.)
Coperion K-Tron
www.coperion.com