Torque control: The other VFD operating mode
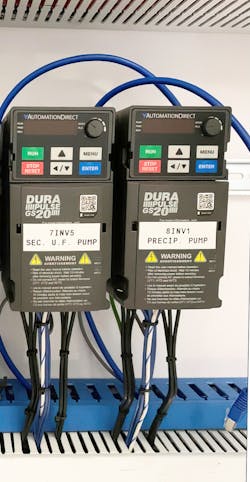
Anyone who has ridden a bicycle is familiar with the fact that the speed at which one pedals and the effort one expends are related but different. It is possible for a rider to pedal at a given speed, but the required torque varies to maintain that speed depending on many factors, primarily path grade — uphill, level or downhill. The same concept applies to AC electrical motors used with machinery and industrial equipment, and it guides the sizing of these motors.
In many cases, the primary concern for an AC electrical motor specification is speed control. Whether a motor is expected to run at a fixed nominal speed, or if a variable frequency drive (VFD) is used to adjust the speed, a designer wants to size a motor of sufficient horsepower to operate the driven load at the commanded speed. VFDs operating in speed mode modulate the power and torque as needed to achieve a commanded speed.
However, there is another class of applications where torque control is the primary goal. Torque control requires a VFD, and it differs from speed control because the primary goal is to operate the motor at a commanded torque, regardless of the resulting speed. VFDs operating in torque mode modulate the power and speed to achieve a commanded torque.
Torque control is a common need for winding and unwinding applications of material rolls in many processing industries, where the diameter of rolled product varies but the tension must be regulated for production consistency. Torque control has formerly been available mostly as a high-end VFD feature, but now has made its way into even mid-level VFD models. Because this capability can now be economically used in more applications than ever, it is important to understand some of its details and benefits.
Torque control applications
Applications for torque control span many industries. Textile processors need to wind and unwind rolls of wovens and webs. The same goes for the pulp and paper industry, and one can imagine how precise the rolling and unrolling balance is for delicate products like toilet paper. But even for metals industries, where flat rolls and wire rolls of steel and other strong materials are involved, the tension must be carefully maintained.
The issue is that the effective diameter of a spool, depending on whether it is rolling or unrolling, varies continuously. If a drive motor applied fixed speed, the effective tension on the product would increase with increasing diameter, and vice versa.
There are other potential applications for torque control, such as with certain material handling equipment, where a designer needs to ensure the mechanical components only experience a certain maximum amount of force, regardless of how the equipment is loaded. It is even possible in certain arrangements for a motor to be energized yet hold a load in a fixed position, with just the right amount of torque, but without any motion one way or the other.
Speed and torque monitoring methods
Motor speed control is most accurately achieved using an additional sensing device, like an encoder, to provide closed-loop feedback. But the reality is that AC motor speed control for many applications can be handled without a dedicated sensor, instead using technologies to imply or indirectly detect the speed.
In North America, a common 480VAC 3-phase 60Hz motor runs at full nameplate speed — typically 1,800 rotations per minute (RPMs), but this varies depending on how many poles the motor has — when it is driven at full voltage and frequency. A standard V/Hz drive control scheme uses this information to command the motor to an approximation of desired speed in an open-loop manner. For instance, 50% speed can be achieved for the noted motor at 240VAC and 30Hz. All VFDs — ranging from micro to general-purpose to high-performance can operate in this mode to control speed.
More advanced VFD designs, and some mid-range general-purpose models available today, use sensorless vector which is not quite closed-loop, but certainly performs better than fully open-loop methods.
Sensorless technology first requires the VFD to “learn” the motor characteristics via a tuning process. Once this is established, the VFD monitors voltage and current of the motor leads in operation to mathematically determine the motor speed with good accuracy.
Getting back to torque control, it is important to understand that output motor torque is proportional to motor current. Flux vector VFDs are best at providing this because the current output is a complex number with a magnetizing current component and a torque current component. However, sensorless vector drives can estimate the scalar value of the current accurately enough for most applications.
VFDs with torque control capability can be tuned to the motor that they control, and then commanded to operate at a desired torque, regardless of the resultant speed, but setting up these VFDs requires a few more steps than for basic devices.
Software support
VFDs used for torque control require some of the same basic setup as those used for speed control. Users must use the device’s keypad, or associated software, to enter the rated frequency, voltage, amps, power, speed and poles for the motor, as well as the maximum allowable frequency. The latter value can exceed the faceplate value in some instances, or it may be clamped at a lower value if desired (Figure 2). Speed limiting is a key feature of torque control. If there is not sufficient torque from the load to meet the torque setpoint, the drive would otherwise quickly accelerate the motor to maximum speed. Utilizing the speed limitation parameters is important to ensure the motor speed does not run away.
Next, the user needs to initiate a “dynamic tuning” of the bare motor, without any pullies or other mechanical components attached. The VFD will spin and stop the motor, energizing it in various ways to determine electrical characteristics such as:
- No load current, in amps
- Stator resistance, in ohms
- Rotor resistance, in ohms
- Magnetizing inductance, in microhenries (mH)
- Stator inductance, in mH
At this point, the VFD has all the information it needs to estimate the motor speed, even without a dedicated speed sensor providing feedback. The user simply needs to put the VFD in torque mode at this point and supply a torque setpoint. This value can be entered via the keypad, but for most applications a 4-20mA signal or a networked value transmitted by a host PLC is the more practical and integrated approach.
Because torque control mode is slightly more involved than basic speed control — although still easily implemented with the right VFD — users should consider whether their chosen VFD brand has some additional features to simplify the task. One example is incorporation of oscilloscope functionality built right into the configuration software (Figure 3).
In most applications, the host automation system, typically a PLC, would send a torque setpoint value as it commands the VFD to run. This signal can vary in operation, and it can do other things, such as being biased with other signals, or clamped and limited in various ways to protect the operating equipment and products.
A torque control loop function block diagram, if available with the VFD, can be a handy tool for visualizing the configuration. This diagram depicts how the parameters interact and what adjustments can be made (Figure 4).
Trouble-free torque control for more applications
Torque control of electric motors is necessary for many industry applications involving any materials being wound or unwound, and it also has other uses for various machinery and equipment applications.
Until recently, torque control has been a more sophisticated mode of operation requiring high-performance VFDs. However, this has changed as some of today’s more economical general-purpose VFDs now offer sensorless vector technology and built-in torque control modes. Combined with easy-to-use configuration and oscilloscope/monitoring software, modern VFDs have made torque control accessible to a much larger range of users and applications.
Kevin Kakascik is a technical marketing engineer at AutomationDirect. Over his 20-year career he has held controls engineering positions for machine OEM’s, entertainment industry systems integrators and material handling systems integrators where he estimated, designed, commissioned and started up systems. Kevin has worked at AutomationDirect since 2013 in technical and marketing roles. He holds a bachelor’s degree in Computer Science and Engineering Technology and an associate’s degree in Electrical Engineering Technology.
AutomationDirect