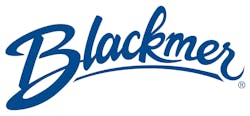
By Geoff VanLeeuwen, PE
Despite their undoubted success in penetrating the seal-less pump market in chemical-processing applications, centrifugal and gear pumps have inherent design and operational attributes that create challenges for the user. These users should be aware of these characteristics when designing systems and selecting pump technologies. In short, chemical-transfer applications are rarely pristine and can be very unpredictable, often leading to pervasive system outages and equipment failures if the proper pumping solution is not deployed.
Sliding vane pumps have proven their standing as a first-choice alternative to centrifugal and gear pumps in chemical-transfer applications because they are simple to use, reliable and flexible. They don’t require tuning to a single BEP; the vanes self-compensate for wear, sustaining like-new performance throughout the system’s operational life; and they can easily handle pumping conditions that feature varying system pressure, zero NPSHa, liquid/vapor mix, suspended solids and regular dry-run operation.
The latest advancement in seal-less magnetic drive technology is the MAGNES Series Sliding Vane Magnetic Drive Pumps from Blackmer®. Offering a world-first combination of functionality, reliability and flexibility, the MAGNES Series delivers performance in severe-duty liquid transfer for high-value chemical-processing applications.
MAGNES Series Magnetic Drive Pumps solve legacy pain points with technically superior functionality that’s designed for chemical and severe duty applications. Key attributes include:
- Indefinite Dry-Run Capability: The MAGNES Series pumps eliminate sensitivity to intermittent, extended and unexpected dry-run conditions. In contrast to pumps that boast of cumulative allowances, MAGNES has an indefinite dry-run range. Imagine the flexibility of being unaffected by poor operating conditions and operator error. Consider the increased functionality of self-priming, suction-lift, product-recovery and line-stripping operations.
- Solids Handling: Unlike most competing technologies that self-destruct when confronted with contaminants, the MAGNES Series Pumps can effectively process liquids with suspended-solids levels of up to 20%.
- Low to Zero NPSHr – Cavitation & Vapor Mixtures Handling: Performing as a zero-NPSHr solution, the MAGNES Series Pumps are ideal for challenging pump inlet conditions, offering sustained performance with liquids featuring up to 20% vapor or air content.
- Full-Curve Performance: Unlike alternate options that must be tuned to a single BEP, the MAGNES Series Pumps have the robustness and flexibility to handle multiple changing fluid and system conditions. In other words, MAGNES provides the flexibility to operate across the full range of chemical-transfer systems.
- Zero Leakage: The containment shell is the foundation of a pump’s leak-free capabilities. The MAGNES shell is unlike any currently available, as it offers dry run, unmatched pressure containment, maximum coupling rating and leak-free operation.
- Zero Alignment: With optional close-coupled drive design, MAGNES enables quick and easy system setup, eliminating time-consuming alignment processes.
- Self-Priming Operation: With suction-lift capability exceeding 25 feet (7.6 meters), sliding vane pumps offer new functionality, reduce additional system operating costs and enhance safety for all operators by eliminating the need to pre-prime the system.
- Product Recovery: Adds line-stripping ability that reduces product waste during or after production runs, recovering the cost of expensive liquids and enhancing safety for plant operators and their staff.
The evolution of the seal-less leak-free sliding vane pump has reached its next level with the development of the MAGNES Series Sliding Vane Magnetic Drive Pump from Blackmer. This innovative new pump technology eliminates the pervasive pain points of legacy centrifugal and gear pumps in chemical-transfer applications. Namely, it has indefinite dry-run capability, can handle solids, operates well with cavitation and vapor mixtures, and offers full curve and system performance. Combine these features with a next generation seal-less magnetic-drive design and chemical manufacturers have a revolutionary new option when searching for the best pump to deploy in their critical and severe-duty operations.
About Blackmer:
Blackmer® is the leading global provider of innovative and high-quality positive displacement, regenerative turbine and centrifugal pump, and reciprocating compressor technologies for the transfer of liquids and gasses. For more than a century, the Blackmer name has stood for unparalleled product performance, superior services and support, well-timed innovation and a commitment to total customer satisfaction. Supported by a worldwide network of distributors and original equipment manufacturers, Blackmer pumps and compressors are used in a multitude of applications in the Process, Energy and Military & Marine markets. Blackmer—headquartered in Grand Rapids, Michigan, USA—is part of PSG®, a Dover company. For more information on Blackmer, please go to blackmer.com.