Proactive plant safety: Identifying risks and implementing smarter solutions
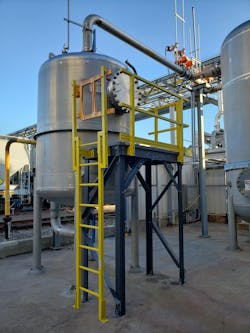
In industrial processing environments, safety is not just a regulatory requirement — it is a foundational pillar of operational efficiency. When safety protocols fail, the consequences range from minor injuries to catastrophic incidents, not to mention significant financial and reputational losses. The stakes are high — that is why proactive safety planning and smart investments are critical to protecting workers and keeping operations running smoothly.
A review of OSHA’s Top 10 most frequently cited safety violations in FY 2024 highlights persistent problem areas across industrial facilities. These violations point to where safety systems are either lacking or not being properly maintained — many of which are entirely preventable with the right planning and infrastructure.
- Fall Protection – General Requirements: 6,307 violations
- Hazard Communication: 2,888 violations
- Ladders: 2,573 violations
- Respiratory Protection: 2,470 violations
- Lockout/Tagout: 2,443 violations
- Powered Industrial Trucks: 2,248 violations
- Fall Protection – Training Requirements: 2,050 violations
- Scaffolding: 1,873 violations
- Eye and Face Protection: 1,814 violations
- Machine Guarding: 1,541 violations
From fall hazards and inadequate training to overlooked machine guarding and PPE failures, these issues continue to pose serious threats to worker safety. For processing facilities, the message is clear: Proactive prevention and compliance with these high-violation areas should be a top priority. These numbers underscore the need for facilities to evaluate current practices and invest in long-term safety systems that anticipate risk and build resilience.
Identifying risks before they become violations
Every processing plant faces safety hazards — some obvious, others hidden in day-to-day routines. Many of these risks stem from the physical environment, aging infrastructure or evolving workflows. Spotting them early is what sets proactive safety programs apart and can make the difference between a near miss and a costly violation.
Common safety risks include:
- Fall hazards: Elevated platforms, unprotected edges and slippery walkways.
- Electrical hazards: Exposed wiring, power generation areas and substations.
- Corrosive environments: Harsh chemicals and outdoor exposure degrading structural materials.
- Mechanical hazards: Rotating or moving equipment with entanglement or crush risks.
While these risks may seem familiar, they are often overlooked until an incident occurs. That is why recognizing red flags in your facility is so important. Some warning signs to watch for include:
Slip, trip and fall hazards:
- Warped or cracked flooring in walkways.
- Missing or damaged handrails.
- Oil, water or residue buildup on floors.
- Poorly maintained stair systems.
Electrical hazards:
- Frayed or exposed wiring.
- Blocked access to disconnects or emergency shutoffs.
- Missing lockout/tagout procedures or signage.
- Overloaded panels or temporary fixes that have become permanent.
Corrosive or damaged infrastructure:
- Rust or pitting on metal platforms and supports.
- Deterioration near chemical tanks, drains or outdoor storage areas.
- Discoloration or bubbling paint — often a sign of underlying corrosion.
The best way to stay ahead of these issues is through regular compliance checks and on-site safety assessments and audits. Effective audits should include:
- Scheduled walk-throughs of key operational areas.
- Visual inspections of access systems, PPE use and signage.
- Documentation of findings — both compliant and non-compliant.
- A clear follow-up process to correct deficiencies.
Many facilities also benefit from having a cross-functional team — safety managers, maintenance personnel and plant supervisors — collaborate during inspections. This approach not only improves awareness but also builds a culture where safety is everyone’s responsibility.
By being proactive in identifying these hazards, processing plants can prevent incidents, maintain OSHA compliance and protect both people and productivity.
Choosing the right safety solutions: What to look for
Selecting the right safety systems is not just about replacing what is broken. It is about anticipating risk, adapting to change and choosing solutions that deliver long-term performance and compliance. Whether the need arises from a safety incident, a failed inspection or an operational shift, upgrades should be driven by both practical and regulatory considerations.
Often, the need for new structures becomes clear only after a problem occurs — such as a slip, trip or fall, or damage from equipment such as a forklift. Some areas may not have been seen as hazardous initially but now require railings, stairs or elevated access. Inspections can also uncover non-compliance that demands action. And in other cases, facilities simply evolve — requiring safer, more efficient ways to move over or around equipment that was not originally part of the plan.
Safety systems should align with OSHA regulations such as 1910.23 (walking-working surfaces), 1910.25 (stairways) and 1910.29 (fall protection criteria). Choosing pre-engineered systems that meet these standards simplifies compliance and inspection.
Solutions for common plant safety hazards
In many processing environments, falls remain one of the most common — and preventable — causes of serious injury. The most effective approach is passive fall protection, such as guardrails, stair systems and elevated platforms that provide built-in safety without relying on employee action or harnesses. These systems are especially important on walkways, mezzanines and other elevated surfaces where OSHA mandates fall protection at elevations of four feet or higher.
It is also important to note that OSHA has updated terminology in recent years. What was traditionally referred to as “handrail” in guarding applications is now classified as “guardrail” when protecting against falls. The actual handrail refers to the grab rail on a stair system, which must meet specific height requirements — minimum 36 inches for handrails and 42 inches for guardrails above the walking surface.
Access challenges are another frequent concern, especially in facilities with dense layouts, overhead piping or floor-level obstructions. Modular crossover stairs are a smart solution for navigating over conveyors, ducts or other fixed equipment. These systems preserve workflow efficiency while preventing the need for workers to take longer, less safe routes around equipment. Properly designed crossover stairs must still meet OSHA clearance standards, including indoor headroom clearance of at least 6 feet, 5 inches and appropriate fall protection on any elevated surface. While most crossovers are intended as anchored, permanent structures, their modular nature allows them to be reconfigured or relocated as plant needs change — such as when new equipment is added, access points are redefined or workflows shift.
Materials matter for addressing plant safety challenges
Material selection is critical. Fiberglass-reinforced polymer (FRP) provides built-in advantages over traditional materials: It is slip-resistant, non-conductive, corrosion-resistant and stable in extreme temperatures. These qualities make it a safer, lower-maintenance choice near chemicals, electricity or heat exposure.
Beyond the material itself, functionality matters. Facilities should consider not only the footprint of a platform or stair system but also what tasks will be performed on it. If maintenance work is common, stairs may be preferable to ladders to provide safer, more ergonomic access — especially when tools or equipment need to be carried. Obstructions such as piping, ductwork or electrical conduits may also drive the need for custom crossovers that help personnel move safely through tight or complex spaces.
Quality and reliability should be non-negotiable. Choose systems backed by manufacturers who have a track record of standing behind their products and who are willing to collaborate on solving real-world challenges — not just delivering a part number. Domestic availability, reputation for performance and engineering support all contribute to a better long-term investment.
FRP plays a key role here as well. Unlike steel, wood or aluminum, FRP is non-conductive, corrosion-resistant and thermally stable. It does not transfer heat or cold to the touch — an important safety benefit in extreme temperature environments — and it will not rust, warp or degrade when exposed to moisture, chemicals or UV light. This durability translates to fewer replacements and less maintenance over time. In addition to its physical advantages, FRP systems are manufactured with safety features such as molded-in grit for slip resistance and high-visibility, color-contrasting stair tread nosing, which helps workers clearly see where each step begins and ends — reducing trip risks, especially in low-light or high-traffic areas.
Installation without disruption — and built to adapt
For many processing plants, shutting down operations for a safety upgrade simply is not an option. That is why installation considerations matter just as much as the solution itself. Modular systems made from lightweight FRP offer a major advantage: They can often be installed during normal operations without the need for heavy equipment, welding or hot work permits. Pre-packaged kits can be shipped within days and assembled by small teams — saving time, reducing labor costs and minimizing disruption.
Just as important as ease of installation is long-term adaptability. As facilities grow, equipment changes or layouts evolve, modular FRP safety structures can evolve too. Systems can be reconfigured, expanded or relocated as needed, integrating seamlessly with new safety zones or access requirements. Options such as gates, access stairs and guardrails can be added or repositioned without starting from scratch. This flexibility not only protects workers today, but it ensures your safety infrastructure stays relevant as operations continue to change.
Building a safer future starts now
The most effective safety programs are proactive, not reactive. Instead of waiting for an incident or citation, leading facilities identify risks early and invest in systems designed to prevent problems before they happen. This approach strengthens everyday safety while reducing long-term liability and disruption.
Creating a safer environment means choosing durable, compliant solutions that support a culture of safety across the facility. These are not short-term fixes — they are investments in the people and processes that keep operations running.
Every plant faces unique challenges. A thorough on-site assessment or safety audit can uncover vulnerabilities, ensure compliance and provide a clear path forward. Prioritizing safety before it becomes a problem helps facilities avoid setbacks, stay compliant and protect what matters most.